Using Time-Tested Techniques, We Take Pride in Every Sash We Build.
Using Time-Tested Techniques, We Take Pride in Every Sash We Build.
LUMBER SELECTION
Every project starts at the lumber rack. After a rough list is calculated, pieces are sifted through for the best cuts with the least waste.



THE PLANER
Next up is the planer. This massive machine with a large cylindrical blade, takes off chunks of lumber to get the material to the correct width.
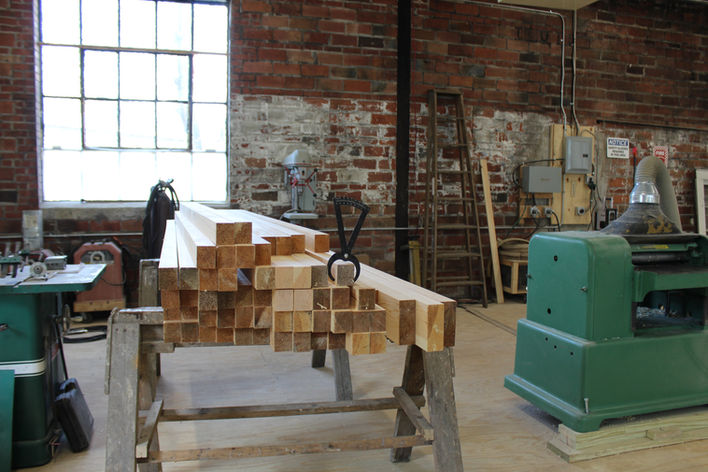
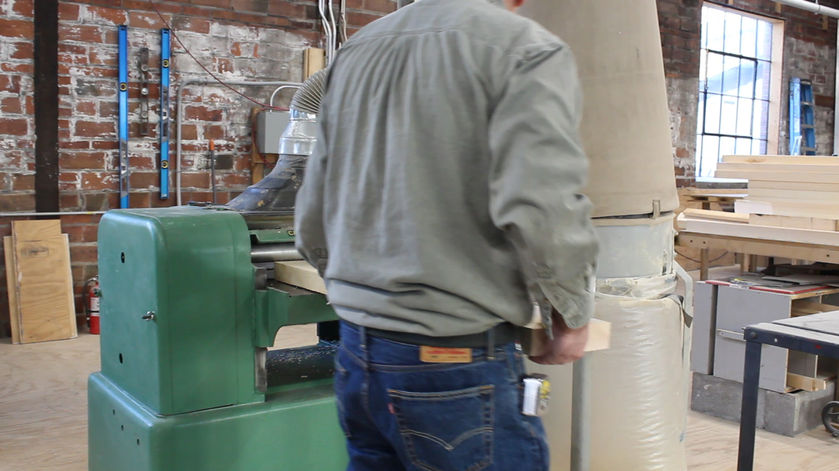
THE SHAPER
Next up is the shaper. This machine cuts both the interior profile and exterior glazng rebate at the same time. Cutter heads can be moved and replaced to fit any shape or style.


THE TENONER
The tenoner was orginally used in wood window manufacturing in the 1950's and 60's. Weighing in at an impressive 1200 pounds, this machines cuts both the cope and the tenon. Members that has been taken to exact (within 1/64" tolerance) dimensions, are run through the tenoner. Video shows muntin tenon and copes being cut.



THE MORTISER
The mortiser is another old piece of machinery. The rails are set up to recieve the mortise, the opening for the tenon.
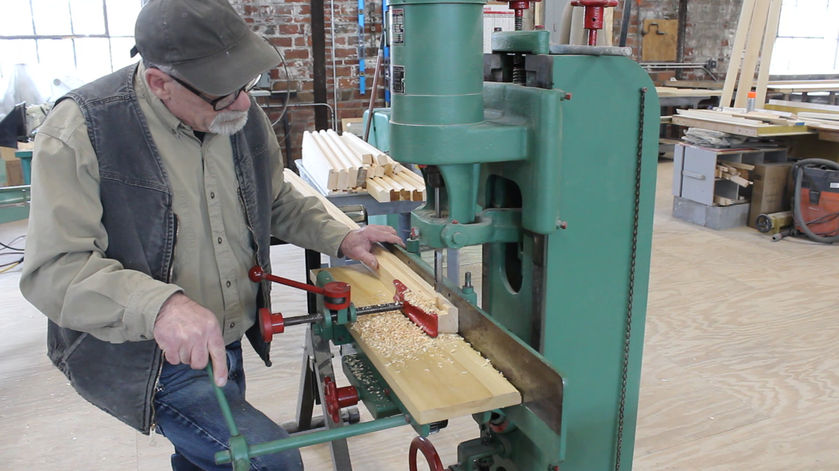
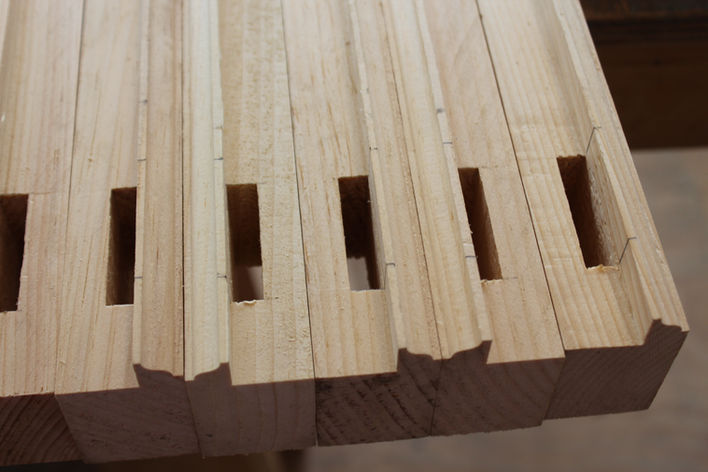
FINAL GLUE-UP
After all the pieces are checked for a perfect fit, the sash pieces are glued together. The mortise and tenon joint holds the sash together, we use glue to minimize water infiltration into the joint.
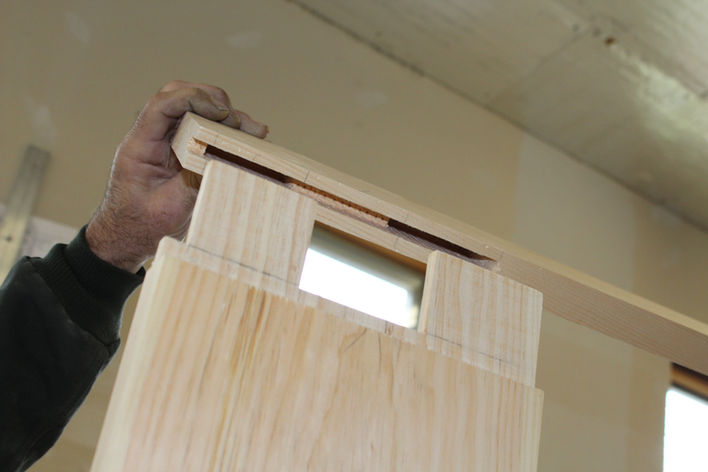
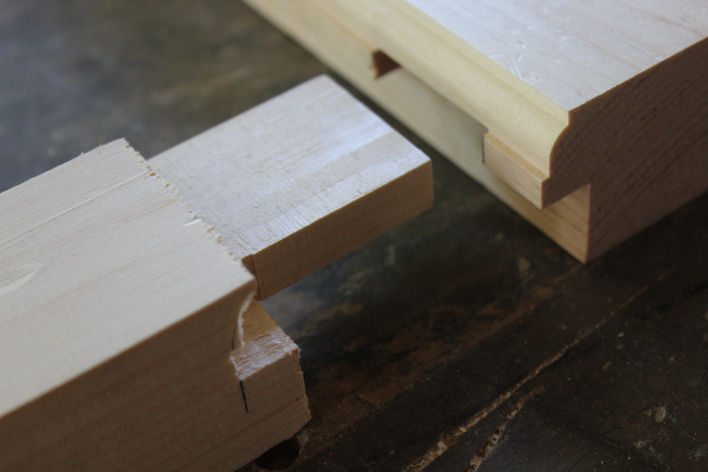
GLAZE AND FINISH
Once the glue has set and clamps have been removed, a light sanding over the whole piece is done for a smooth finish. Then the glass is set, either in glazing putty or silicone. We use an alykd primer for best wood sealing properties and finish with 2 coats of finish paint.
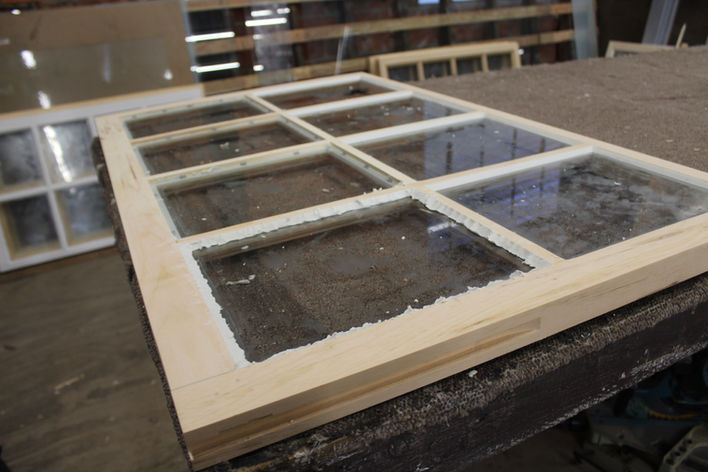
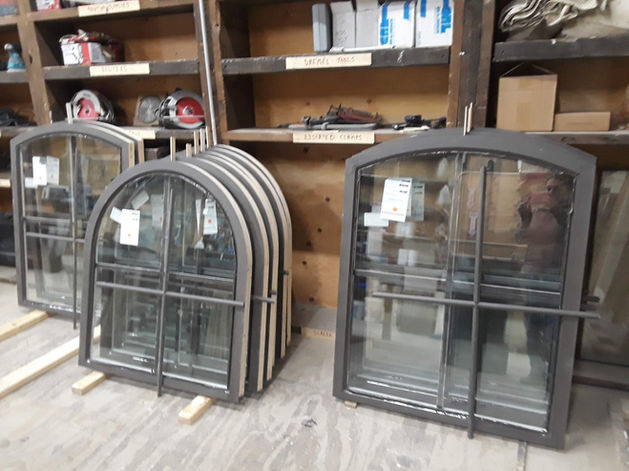